IO-Link Intelligent automation of industrial systems
Nowadays, IO-Link sensors and actuators are key components for efficient and simple communication in industrial automation. With their measured values, STEGO IO-Link sensors enable precise control and parameterisation of applications in areas such as climate detection, distance measurement and current measurement. Find out more about the benefits of IO-Link technology and how it can optimise your automation processes in this blog.
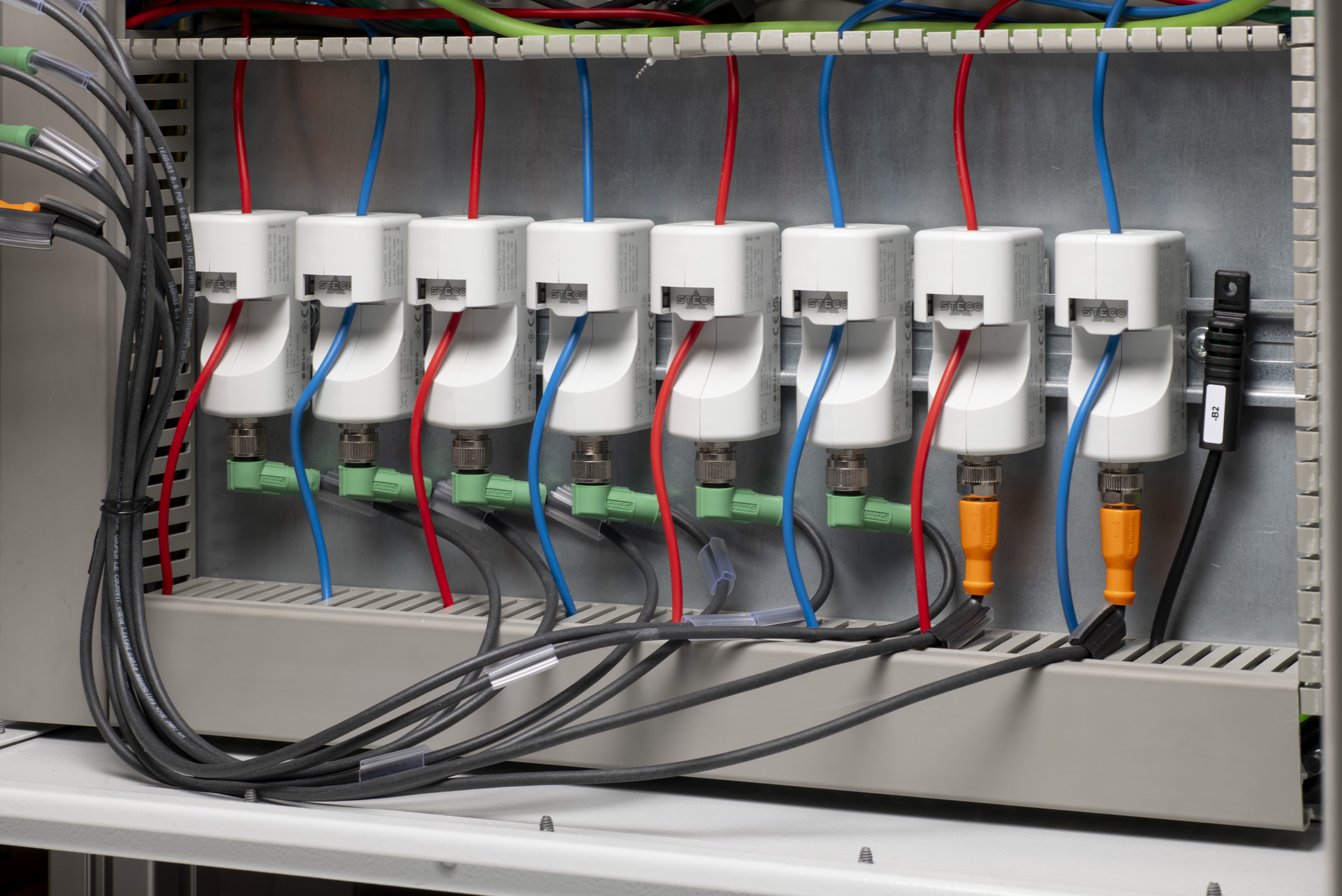
Introduction: What is IO-Link?
IO-Link is a leading standard in industrial automation that enables the simple and efficient integration of sensors and actuators into digital networks. It is a bidirectional communication interface that allows devices to send and receive data.
In contrast to conventional analog interfaces, IO-Link offers digital data transmission, resulting in precise and reliable communication between devices. This transmission takes place via a uniform, standardized interface, regardless of device type or manufacturer, which improves the interoperability and interchangeability of components.
In addition, IO-Link offers a range of functions to increase efficiency and flexibility in production. These include parameterizable device configuration, diagnostic functions for fast troubleshooting and the transmission of additional process and device data. This enables production engineers to comprehensively monitor and control their systems to optimize production processes.
Another advantage of IO-Link is its versatility and flexibility. IO-Link devices can be integrated into almost any fieldbus and control system infrastructure, allowing for easy integration and commissioning. In addition, IO-Link supports the processing of multiple measured values from different sensors simultaneously, resulting in comprehensive monitoring and control of production facilities.
Overall, IO-Link offers a powerful solution for optimizing manufacturing processes through precise and reliable communication, flexibility in the integration and control of devices and a variety of functions such as condition monitoring and remote access.
Purely digital transmission
Maximum reliability
IO-Link offers production engineers the security of reliable data transmission at the highest level. By using a 24 V signal and purely digital transmission, communication between sensors, actuators and the controller is conversion- and loss-free. This means that the transmitted data remains precise and unaltered, resulting in a high level of accuracy and consistency in production.
Elimination of interference factors
Thanks to the digital and conversion-free transmission with IO-Link, potential interference factors are minimized. Signal losses or interference that can occur with analog transmission are a thing of the past. This ensures constant and reliable communication between the devices, even in demanding production environments with strong electrical interference or EMC interference.
Simple integration and commissioning
The use of a 24 V signal and digital transmission make the integration and commissioning of IO-Link devices extremely simple and efficient. As no time-consuming calibration or adjustment is required , production engineers can quickly commission the devices and optimize their production facilities without delay.
Future-proofing and compatibility
IO-Link offers a future-proof solution for production engineers as they benefit from the advantages of digital communication that keeps pace with the latest technological developments. In addition, IO-Link is backwards compatible, which means that older devices can be integrated with new IO-Link systems without the need for expensive and time-consuming upgrades.
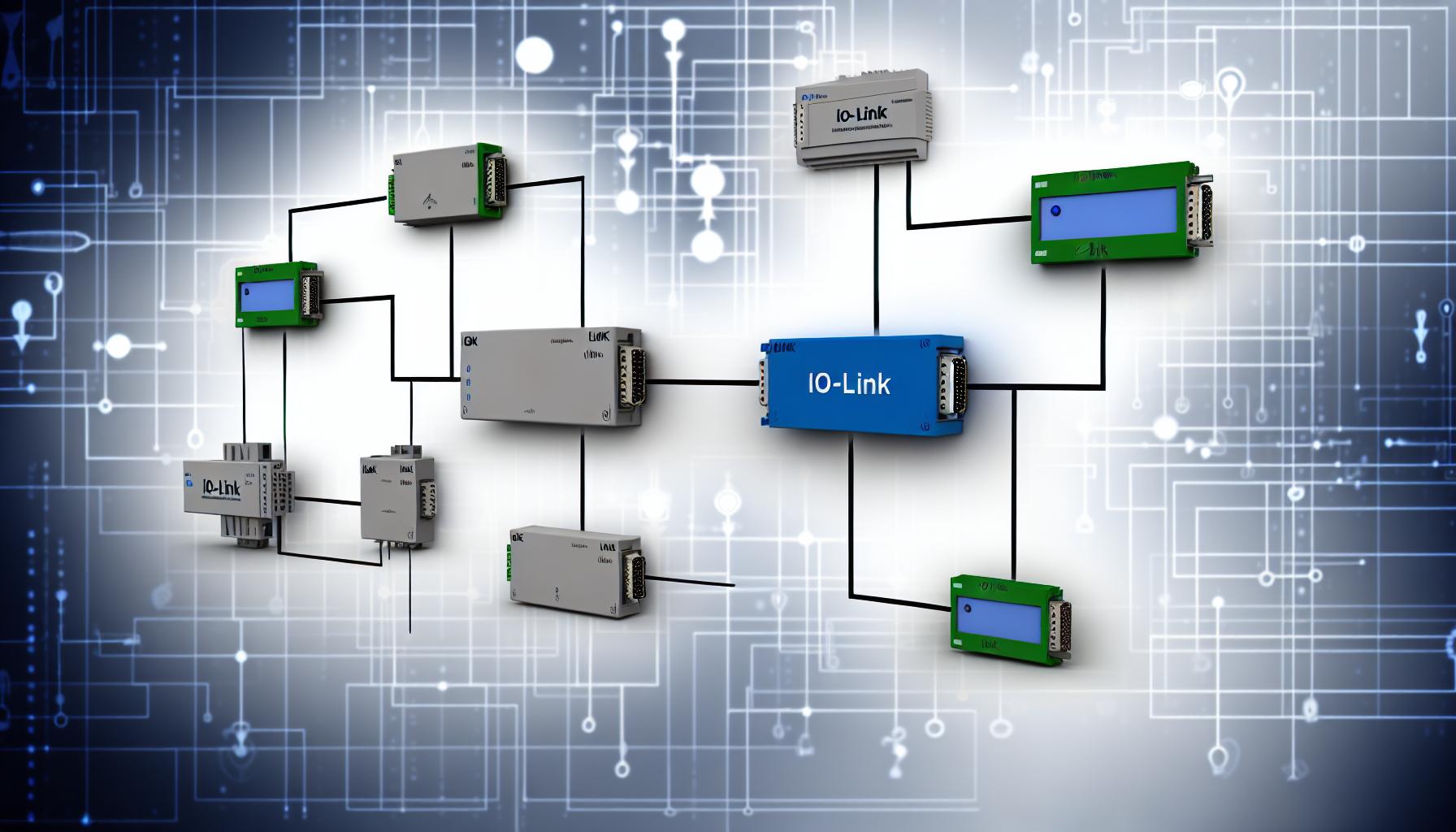
Seamless integration into existing infrastructures
Independent of fieldbus and control systems
Thanks to the flexibility of IO-Link masters, IO-Link devices can be easily integrated into almost any fieldbus and control system infrastructure. Whether Profibus, Profinet, EtherCAT or other fieldbus systems - IO-Link masters offer a universal interface that enables smooth communication between the various components. Production engineers can therefore expand existing systems or add new components without having to make major adjustments or investments in the infrastructure.
Flexibility and scalability
The ability to integrate IO-Link devices into different infrastructures offers production engineers a high degree of flexibility and scalability. They can expand their production facilities as needed to meet new requirements or optimize processes without having to limit themselves to specific fieldbus protocols. This enables agile and cost-efficient adaptation to changing production requirements and helps to future-proof the systems.
Simplified configuration and commissioning
IO-Link masters also considerably simplify the configuration and commissioning of IO-Link devices. Thanks to their intuitive user interface and compatibility with common engineering tools, production engineers can commission the devices quickly and efficiently without the need for extensive programming knowledge. This reduces commissioning times and makes it easier to integrate new components into existing systems.
Compatibility with Industry 4.0 standards
The seamless integration of IO-Link devices into various fieldbus and control systems makes them an ideal solution for Industry 40 applications. IO-Link forms a solid basis for the implementation of intelligent manufacturing concepts, as it enables reliable and standardized communication between all levels of the production environment.
Reduced installation costs
Unshielded cables save costs
The insensitivity of IO-Link signal transmission to external interference offers a considerable advantage in terms of installation costs. By dispensing with shielded cables and the associated earthing, companies can achieve considerable savings in installation costs. As data transmission can be implemented using standard industrial cables (three-core cables), there is no need for expensive special cables, which significantly reduces the overall cost of cabling .
Elimination of digital/analog converters
The use of IO-Link technology also enables considerable savings to be made on equipment parts that are not immediately thought of. By becoming independent of costly analog input cards (digital-to-analog converters), companies can eliminate these components, resulting in direct cost savings. This allows companies to cost-effectively modernize or expand their production facilities without having to make additional investments in expensive input cards.
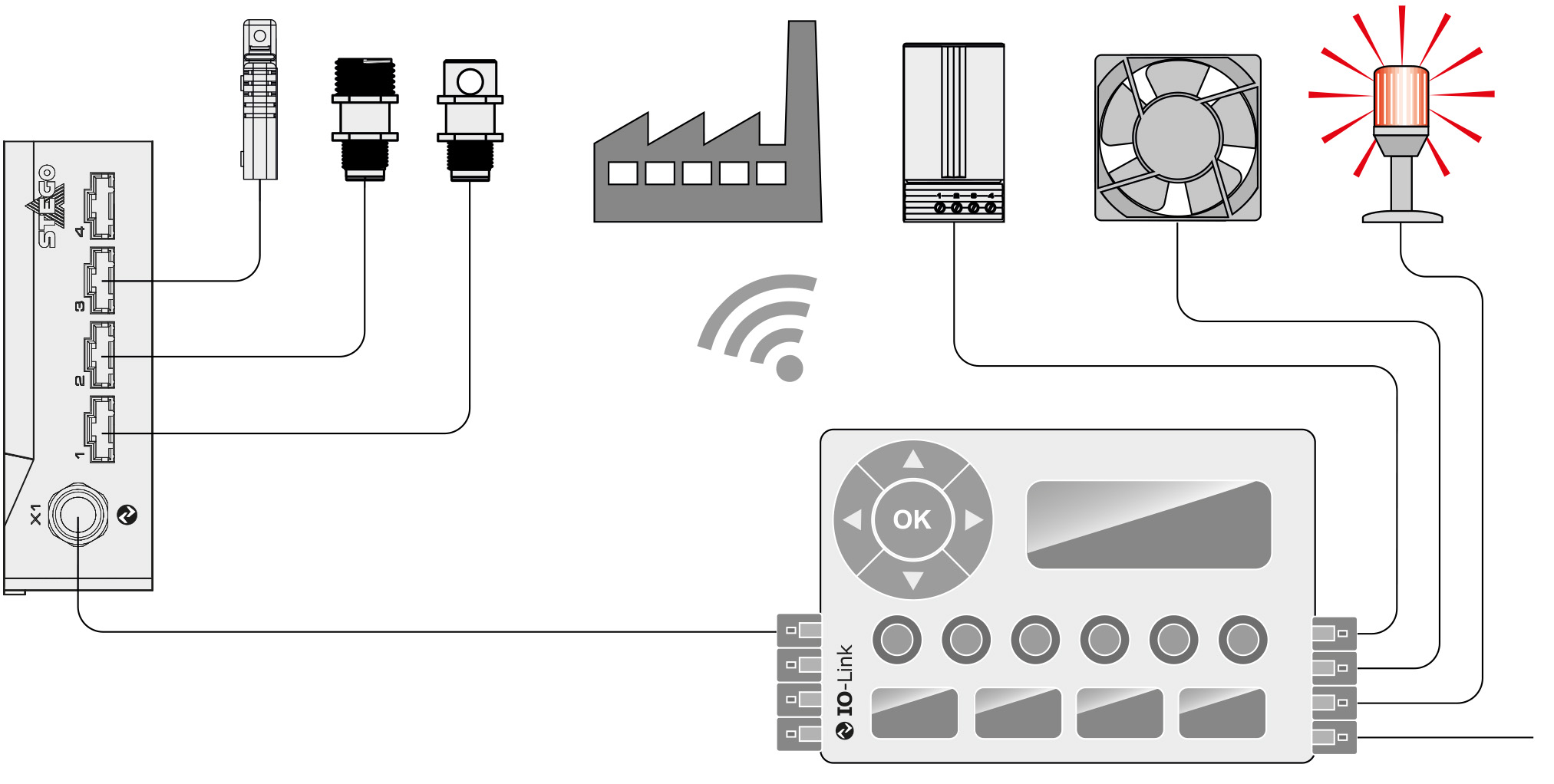
Condition monitoring and remote access
Monitoring in real time
In the field of condition monitoring, IO-Link offers an efficient solution for monitoring system statuses in real time. The ability to process several measured values from sensors simultaneously enables production engineers to gain a comprehensive insight into the condition of their systems. This enables early detection of deviations or potential failures, leading to a reduction in downtime and maintenance costs.
Remote access via the internet
IO-Link also enables remote access to sensor data and system control via the internet. Production engineers can therefore access the systems from any location and make settings or carry out diagnostics without having to be on site. This improves responsiveness and efficiency in the maintenance and optimization of production facilities and helps to increase overall productivity.
The combination of condition monitoring, processing of multiple measured values and remote access via IO-Link offers companies a powerful solution for optimizing their manufacturing processes and maximizing plant availability.
IO-Link sensors from STEGO in use
Climate monitoring with the CSS 014
The Smart Sensor CSS 014 from STEGO is the innovative IO-Link sensor for monitoring environmental conditions in control cabinets. It precisely measures temperature and humidity to ensure optimum conditions for electronic components. With its compact design and simple installation, it offers an effective solution for preventing condensation and damage caused by humidity. The sensor enables reliable monitoring and sets off alarms in the event of deviations, which increases operational safety. Thanks to its intelligent technology, the CSS 014 is an indispensable tool for protecting sensitive devices in switch cabinets and electrical enclosures.
Detect distances with the DSS 015
The DSS 015 from STEGO is a smart distance sensor that uses ultrasonic waves and the principle of time-of-flight (ToF) measurement to determine the distance to objects. This sensor is designed for use in various applications where precise distance measurements are required. It offers a digital IO-Link interface and supports a detection range of 0.3 m to 4 m. The sensor's field of view is conical with an angle of 45°. The sensor works with an operating voltage of DC 24 V (DC 18 - 30 V) and has a maximum power consumption of 0.6 W.
Measuring current with the ESS 076
The STEGO ESS 076 is a smart current sensor for precise measurement of current consumption in industrial systems. It measures AC current up to 100 A without contact and outputs data in analog (4-20 mA) or digital (IO-Link) form. With its high-precision measurement technology, it supports condition monitoring and enables energy efficiency measures and cost reductions by identifying load peaks. The sensor is retrofit-compatible and offers versatile mounting options.