Monitoring Load Peaks with IO-Link Current Sensors
As industries embrace digitalization, new and innovative ways to cut costs are emerging, and one key approach is through energy optimization. A crucial aspect of this strategy involves closely monitoring instances of high energy demand. Unexpected spikes in electricity usage can result in significant additional expenses, particularly in energy-intensive production settings. This is where STEGO's ESS 076 Smart Sensor Current steps in. In this article, we'll explore how this intelligent current sensor, equipped with an IO-Link interface, provides an effective solution for keeping a close eye on load peaks. Not only does it help in monitoring these peaks, but it also plays a role in enhancing overall energy efficiency.
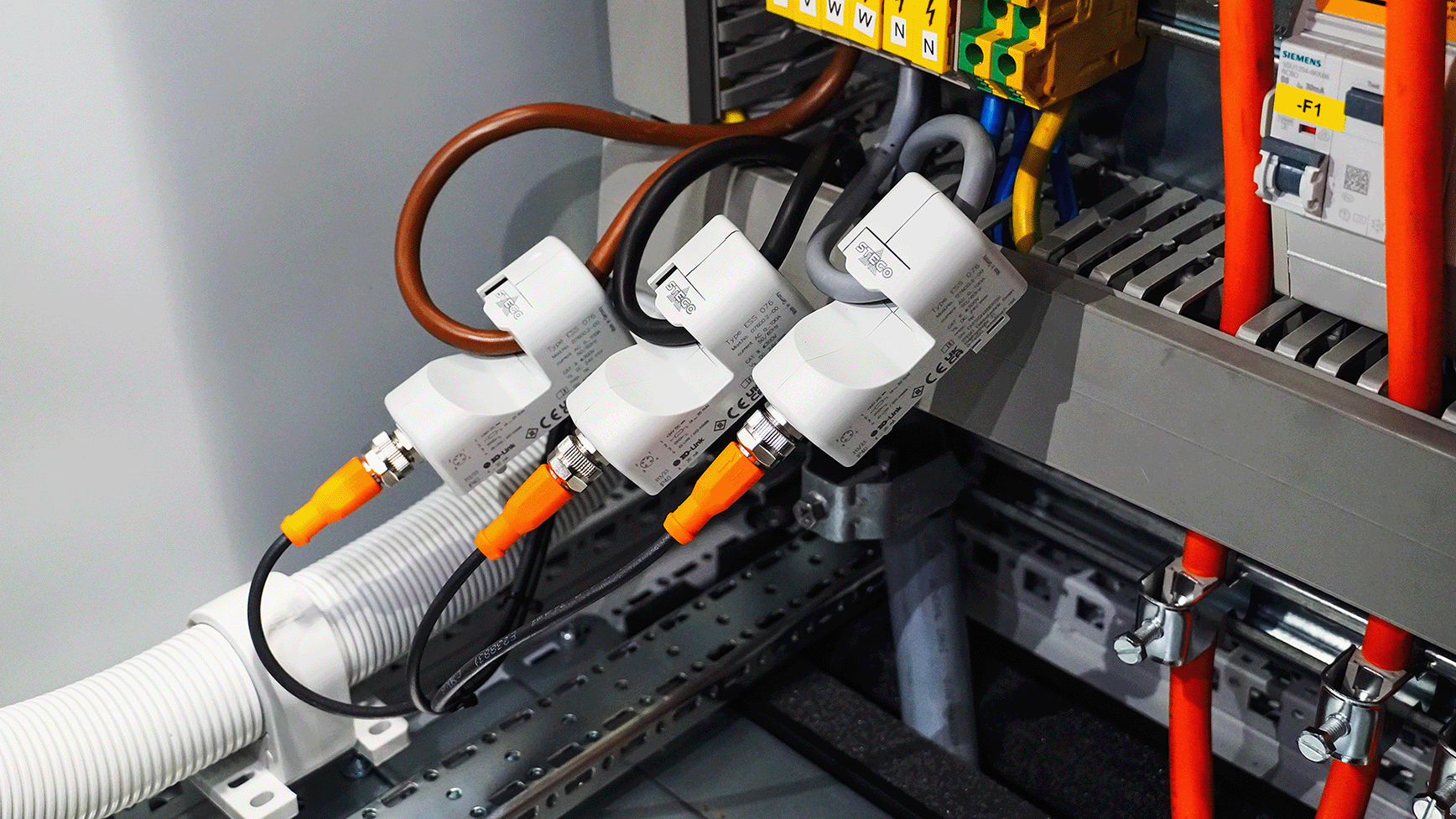
AVOID UNPLEASANT SURPRISES
For manufacturing companies, unexpectedly high electricity bills are among the most unwelcome surprises. December, in particular, can turn into a financial pitfall. Speaking of December: why is this month so crucial when it comes to the total cost of electricity consumption? The reason is that a high peak load in December can result in a subsequent increase in electricity costs for the entire year, imposed by the grid operator. But what if there was a way to avoid these unpleasant surprises? Combine the measuring of electricity consumption per machine and employing peak shaving – a you get a smart strategy to recognise peak loads and shield yourself from unwanted additional payments. This article dives into how precise electricity measurement, especially with the ESS 076 Smart Sensor Current from STEGO, holds the key to a stress-free year-end.
MONITOR ELECTRICITY IN REAL TIME
Current sensors like the ESS 076 offer straightforward real-time monitoring of power consumption in systems and machines. The potential for efficiency gains is significant, especially in energy-intensive applications. This becomes evident in our case study with our client, LEGROM. Specializing in plastic injection molding, LEGROM operates an extensive array of injection molding machines, known for their high energy demands as they heat and process plastic granules under high pressure.In the past, the immediate or simultaneous activation of injection molding machines at LEGROM resulted in unexpected additional electricity costs. Retrofitting the machines with a current sensor proved to be a much more cost-effective solution compared to dealing with additional payments. This is crucial, considering that in an industrial setting, these extra electricity costs can quickly escalate into five-digit euro sums.
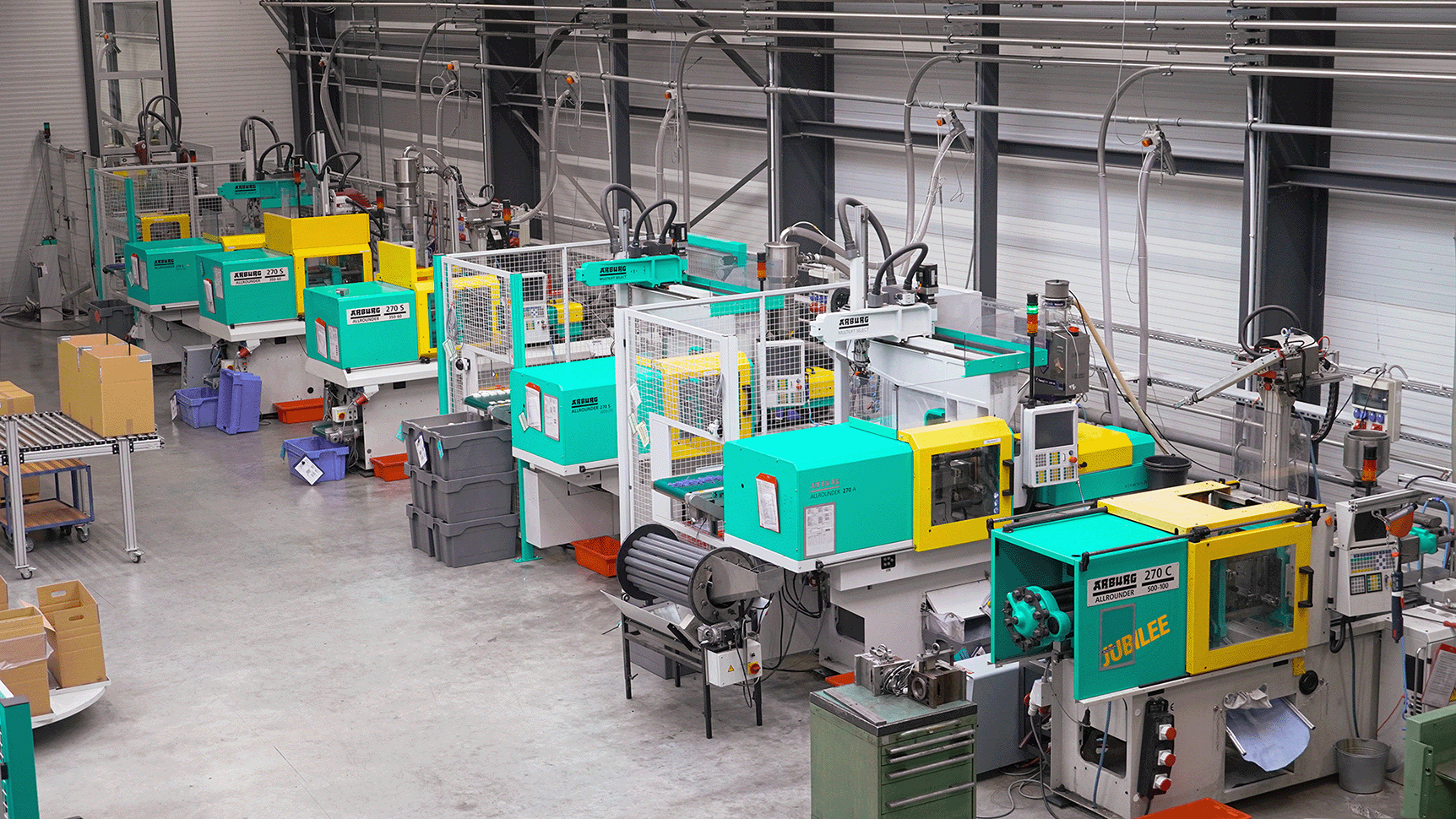
CURRENT SENSORS FOR THE RETROFIT
From the outset, LEGROM recognized that advancing energy flow monitoring would depend on peak shaving. Kim Waldmann, Managing Director at LEGROM and an industry expert in injection molding, drew on his experience across various injection molding companies to understand that information is the key resource for more efficient processes and risk mitigation.
For LEGROM, the digitization process was carefully planned as a well-thought-out use case. However, the approach needed to be "minimally invasive."
An intelligent retrofit application for current measurement became crucial for their operational technology (OT). Integrating sensors into the numerous machines in the injection molding shop floor had to be quick and straightforward to minimize both time and complexity. The goal was to keep machine downtimes to a minimum to avoid disruptions to production capacity and productivity. Waldmann explained, "The integration of the STEGO current sensors was uncomplicated. We only needed to disconnect the machines from the power supply and route the live cable through the ESS 076. The sensor can measure up to 100 A AC without direct contact, perfectly fitting our current condition monitoring needs. The sensors’ practical latching mechanism ensures secure and simple attachment to the power line."
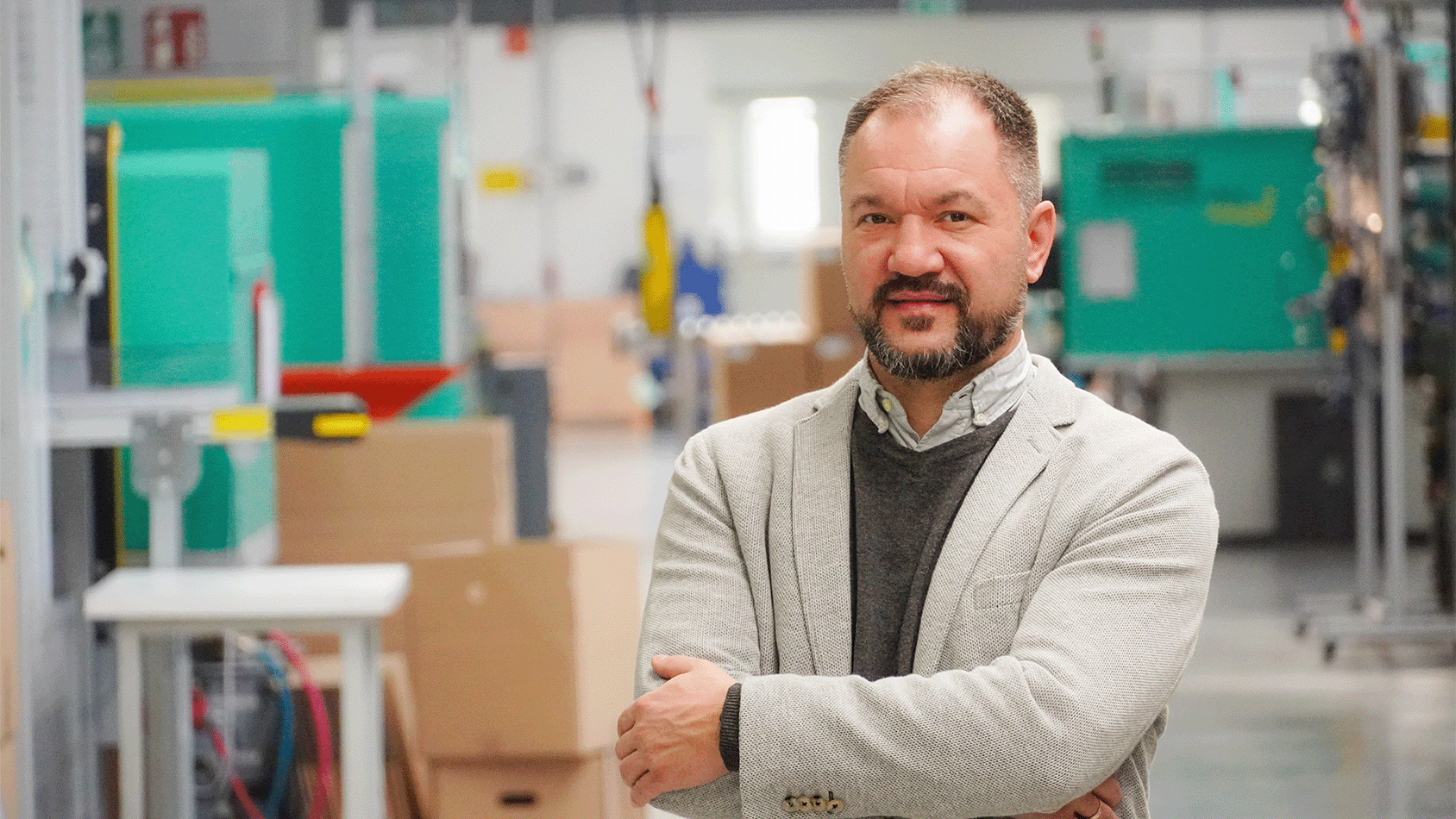
CONSTANT DATA FLOW WITH IO-LINK
LEGROM chose the ESS 076 current sensor for its groundbreaking features, previously unavailable in the market. Notably, it boasts two interfaces: an analog and a digital one, rendering it highly versatile in a wide array of applications. Its analog functionality, with the robust 4-20 mA signal, makes it suitable for almost any application. However, the real ingenuity lies in the integrated IO-Link interface, where the full potential of IO-Link unfolds. The advantages are particularly enticing for experts, offering significant added value in industrial production environments:
- Versatile Connectivity: IO-Link sensors facilitate standardized communication between sensors and control systems. This versatility eases integration into different systems and enables flexible configuration. In the case of the injection molding machines, sensor data could be directed to LEGROM's IoT platform for condition monitoring.
-
Automated Parameterization: IO-Link sensors are virtually plug & play ready for use. Parameterization is automated and yet flexible, allowing adjustments to meet the specific requirements of each injection molding machine in the IO-Link software. This facilitated a swift and efficient deployment of the sensor assembly in LEGROM's shop floor.
- Diagnostic and Status Information: The sensor's ability to provide diagnostic and status information is a key aspect. This simplifies real-time monitoring of the sensor status, leading to improved maintenance and reduced downtime. Moreover, the ESS current sensors provide crucial measured values for energy and power via their IO-Link interface, transmitted to the achtBytes IoT platform that LEGROM uses for condition monitoring.
- Integration in Industry 4.0 Environments: Modern IO-Link sensors like the intelligent ESS 076 seamlessly integrate into Industry 4.0 environments. This enables networked production where data is efficiently used to optimize processes and enhance overall performance. The ESS 076 current sensors, coupled with the SaaS IoT platform from software provider achtBytes at LEGROM, form a powerful alliance, providing detailed real-time insights into the energy situation of the machinery for those in charge at LEGROM, aligning with an energy grid perspective.
ESS 076 - IO-LINK CURRENT SENSOR FOR EFFICIENT ENERGY USE
In energy-intensive production setups within industrial environments, the adoption of these intelligent sensors proves to be a swift return on investment. The cost-effective solution of current sensors minimizes the risk of unforeseen additional electricity costs. Leveraging the IO-Link technology of the ESS 076 ensures seamless integration into Industry 4.0 applications, providing user-friendly operation and connectivity.
Thanks to plug & play functionality, the ESS 076 current sensors are particularly well-suited for long-term monitoring through time series. The combination of low costs and minimal maintenance makes the ESS 076 the ideal choice for comprehensive current monitoring. Explore the advantages of efficient energy monitoring with IO-Link current sensors from STEGO.